Szűcs Miklós: Korszerűsítés a vasbetonaljak gyártásában
Az előregyártott betonelemek gyártása és a telepítés helyszínére való szállítása csökkenti az építési időt, és lehetővé teszi a telepítés gyorsabb, illetve hatékonyabb elvégzését, mérsékelve a környezeti hatásokat és az építési terület nagyságát. A vasúti alj egy fontos eleme a vasúti infrastruktúrának. A vasúti alj gyártása egy olyan terület, ahol általában lassúak és időigényesek a technológiai fejlesztések. Azonban az elmúlt években ezen a területen is egyre inkább megjelennek a modern technológiák és az innovációk. A modern technológiák használata lehetővé teszi, hogy a vasúti aljat gyorsabban, hatékonyabban és pontosabban hozzuk létre, miközben csökkentjük a környezeti hatásokat és javítjuk a vasúti alj minőségét. Ebben a cikkben bemutatok egy fontos, a gyártásban nélkülözhetetlen gépet, amelyet a közelmúltban lecseréltünk.
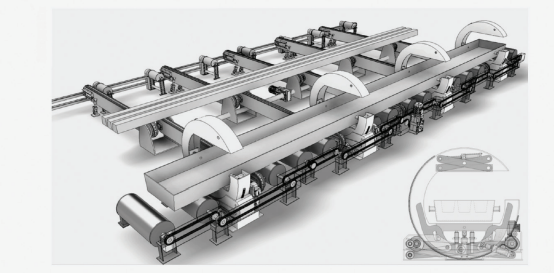
1. kép: A borítógép tervezés alatt
A lábatlani gyárat 1942-ben alapította kilenc részvényes kétszázötvenezer pengő alaptőkével. Kezdetektől fogva a vállalat fő profilja az előregyártott mélyépítési vasbeton elemek és vasúti aljak gyártása volt. Az üzemet 1948-ban államosították, ezt átszervezések, összevonások, majd tevékenység-leválasztások követték. A kisvasúti betonaljak gyártása 1949-ben, az előfeszített vasbeton aljaké 1958-ban indult meg. 1964-től mezőgazdasági, 1966-tól pedig már építőipari termékek is készülnek Lábatlanon. Az 1980-ban átadott központi gyártócsarnokban feszítettvasútialj-gyártó technológia létesült. Majd európai viszonylatban is az elsők között, 1984-ben elkezdődött a beton vasúti kitérők és átmeneti aljak gyártása.
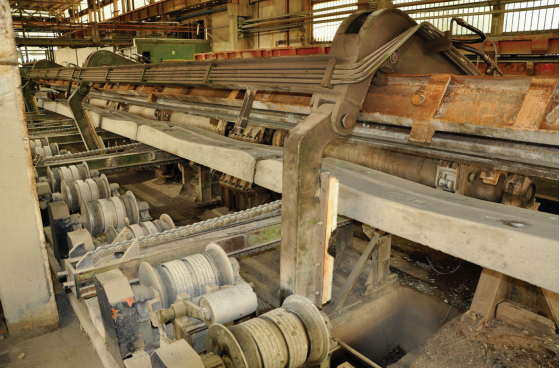
2. kép: A régi alj borítógép
A technológia évi 380.000 darab alj legyártására képes. A gyártás félhosszú pados elrendezésben történik. A vasúti alj gyártástechnológia egyik fontos része a késztermék elválasztása a sablontól. A művelet során a 6-7 tonnás sablonokat a hossztengelyük körül 180°-kal el kell forgatni. Erre a műveletre az elődeink egy szellemes – az akkori kornak megfelelő – megoldást alkalmaztak. Két együttműködő hidraulikahenger egy fogaskerék-fogasív áttételen keresztül tudta a sablont termékestől átfordítani. A sablon két oldalának alsó peremét 6 db hidraulikus pofa fogta a fordítás alatt, míg a termékeket 3 db reteszelhető kar tartotta a helyükön. Az átfordulás után a karok elengedték a termékeket, amelyek egy láncpályára érkezve folytatták útjukat. Mivel a termék a feszültségoldás hatására az előző munkahelyen egy picit megmozdult, ezért szinte mindig sikeres volt a kiborítás folyamata. A 2. képen látszik, hogy a forgatás tengelye nem esik egybe a sablon hosszirányú súlyvonalával, ezért a forgatáshoz szükséges nyomaték igen nagy volt. Ez jelentős teljesítmény-felvétellel és az erőláncban részt vevő elemek intenzív kopásával járt együtt. A legkritikusabb a hidraulikus hengerek kopása és a fogasív sérülései voltak. A fogasív igen speciális, nyíl fogazású volt, amelynek felújítása egyre nehezebbé vált.
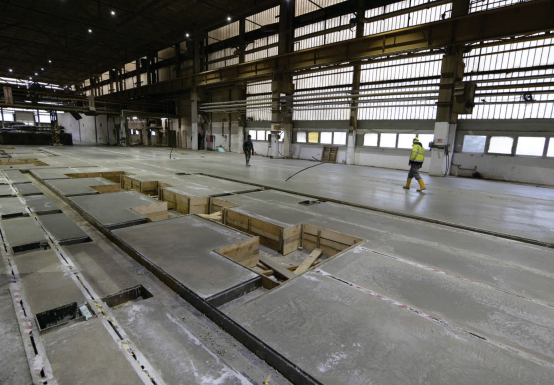
3. kép: Az új borítógép alapozási munkái 2020-ban
Ilyen körülmények között – a mai kornak megfelelve és a termelés biztonságát biztosító technológia-felújítás keretében – döntöttünk eme patinás gépünk lecseréléséről 2019 elején. Az új gép beszerzését hosszú egyeztető folyamat előzte meg. Az időzítése pedig egybeesett a fő gyártócsarnokunk BETONELEMGYÁRTÁS Korszerűsítés a vasbetonaljak gyártásában SZŰCS MIKLÓS TERMELÉSI IGA ZGATÓ, L ÁBATL ANI VASBETONIPARI ZRT. gyártópadlójának teljes cseréjével. A csarnok padlójának cseréjével együtt az új gép alapozását is el kellett végeznünk.

4. kép: PLC vezérlés HMI-vel az új borítógépen
A tervezésnél fontos szempont volt a könnyű szerelhetőség, az alkatrészek tipizálása, továbbá a korszerű gép- és vezérlési elemek alkalmazása. A gyártott termékek sokfélesége miatt a forgatónak az összes meglévő sablontípussal kompatibilisnek kellett lennie. Ez a sablonváltozatosság a gyártott aljak eltérő hosszából, magasságából, síndőléséből, nyomtávjából és a sín lekötésének típusából adódik. Hiszen gyártunk aljat normál nyomtávra (1435 mm), keskeny nyomtávra (760 mm) és szélesre (1520 mm) is. Az egyeztetés alatt előzetesen több lehetőség is felmerült. A tervezés egy közbenső állapota látható az 1. képen.
Az új forgatóegység a mai kornak megfelelő PLC-vezérléssel és a hozzá tartozó kezelőfelülettel (HMI) készült. A program információt ad az esetleges elakadásokról, a kijelzőn nyomon követhető a sablonkiborítás minden fázisa. Alkalmas a sablonok számolására, valamint az ütemidők rögzítésére. Ezekből a gyártás hatékonyságára és az egyes aljtípusok gyártási idejére lehet következtetéseket levonni. Ez különösen fontos abban az esetben, amikor sokféle típusú aljat gyártunk különféle sablonokban egyazon műszakban.
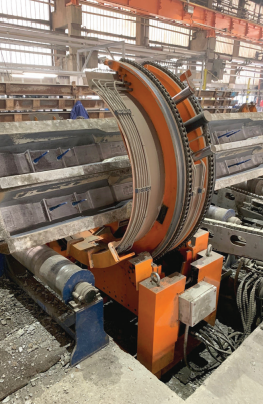
5-6. kép: Az új borítógép működés közben
A sablon forgatási középpontja szinte megegyezik a súlyvonalával, így igen kevés erő és energia kell a művelet elvégzéséhez. A C alakú megfogóív lánchajtással mozog a megvezető görgőkön, melyek a váz oldalát is tartják. Az egész szerkezet pedig egy ollós mechanizmussal emeli el a sablont a behordó görgősorról. Az összetett mozgások egymásutániságát érzékelők biztosítják.
Gyárunk tehát megújul, hiszen még sok aljat kell legyártanunk a jelenlegi és a jövőbeli projektekhez. A versenyt pedig bírnunk kell. Ebben jól állunk, hiszen az anyacégünk világszerte (Németország, USA, Szaúd-Arábia, Spanyolország, Románia, India, Korea, Törökország…) telepített gyárai között is kiválóan megálljuk a helyünket.
(fotók: a szerző)